Medical Device Preventative Maintenance
-
Preventative Maintenance
Medical Device Preventative Maintenance
-
Preventative Maintenance
identify potential device failures with the trimedx predictive work system
Unexpected breakdowns of high-volume imaging equipment can lead to frustrated patients, unhappy clinicians, and significant lost revenue. With advanced medical device preventative maintenance technology and expertise from TRIMEDX, you can detect potential failures before they occur and reduce unplanned downtime.
There is never a good time for medical equipment to break down, especially in critical, high-volume imaging departments.
TRIMEDX Predictive Work System (PWS)
TRIMEDX Predictive Work System (PWS) streamlines medical device preventative maintenance by adding an extra level of vigilance in monitoring for warning signs of potential failures. Health systems can reduce the burden on clinical staff and biomed teams by reducing unexpected disruptions to clinical operations and maintenance schedules caused by emergency repair needs.
IDENTIFY Preventable Failures
- Remote device monitoring
- Event detector algorithms
- Data science
DETECT Device Problems
- Automated work orders
- Prescribed remediation
RESPOND Proactively
- Department collaboration
- Scheduled downtime
%20Definition.jpg)
PWS Outcomes
By combining remote device monitoring, service expertise, and data science, PWS identifies common preventable equipment problems before a failure occurs. PWS automatically issues 'smart' work orders with prescriptive repair actions, relevant parts, and service manual information. Technicians can schedule medical device preventative maintenance at a time that is convenient for clinicians and patients. As an innovative feature offered with the TRIMEDX comprehensive Clinical Engineering solution, PWS helps health systems worry less about equipment failure and focus more on patient care.
- Reduce unplanned downtime with scheduled repairs
- Improve patient experience and safety
- Increase clinician satisfaction
- Avoid revenue loss
- 1,000 downtime events are diverted or avoided annually1
- 31K+ hours in unplanned downtime avoided annually1
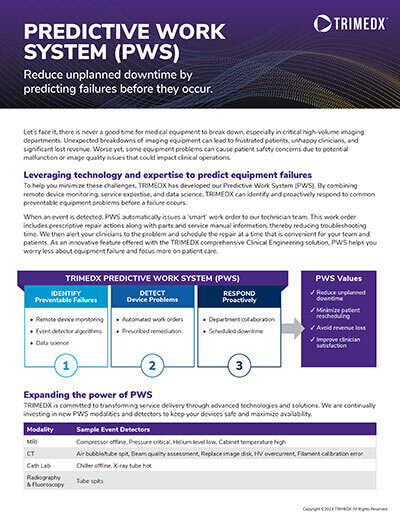
PWS in Action
A wide variety of healthcare organizations have deployed PWS to reduce unplanned downtimes and streamline medical device preventative maintenance. See some examples below of what these health systems have achieved.
PWS USE CASE:
Predicting Air Bubbles In CT
Problem: The presence of air bubbles in CT machines is a well-known, but hard to predict, problem that can cause artifacts, misdiagnosis, administration of excess x-ray doses, and lost revenue opportunities. At a hospital in the Midwest, the CT appeared to be functioning normally to the radiologic tech. However, there were view-corrections, tube arcs, and air bubbles developing within the CT.

Solution: With PWS, TRIMEDX was able to detect the air bubbles and schedule a repair with the client during non-patient hours that:
- Avoided 48+ hours of unplanned repair downtime
- Prevented tube damage and high-voltage component replacement
- Ensured clinical uptime when needed most
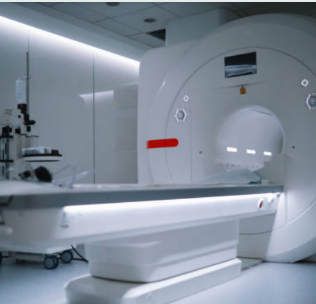
PWS USE CASE:
Detecting Offline MRI During Closed Hours
Problem: A power outage shut down an MRI at a standalone imaging center on a Sunday night when the center was closed.
Solution: PWS detected the loss of power to the MRI and generated a work order. The TRIMEDX technician was able to communicate the outage to building security, and once power was restored, the technician reset the MRI power and brought the system up, which:
- Minimized disruption to the scanning schedule since the MRI was ready Monday morning
- Avoided patient inconvenience and rescheduling
- Reduced clinician and staff frustration
- Prevented excessive helium boil off
Explore TRIMEDX's clinical engineering service solutions
FOOTNOTE
1TRIMEDX internal data